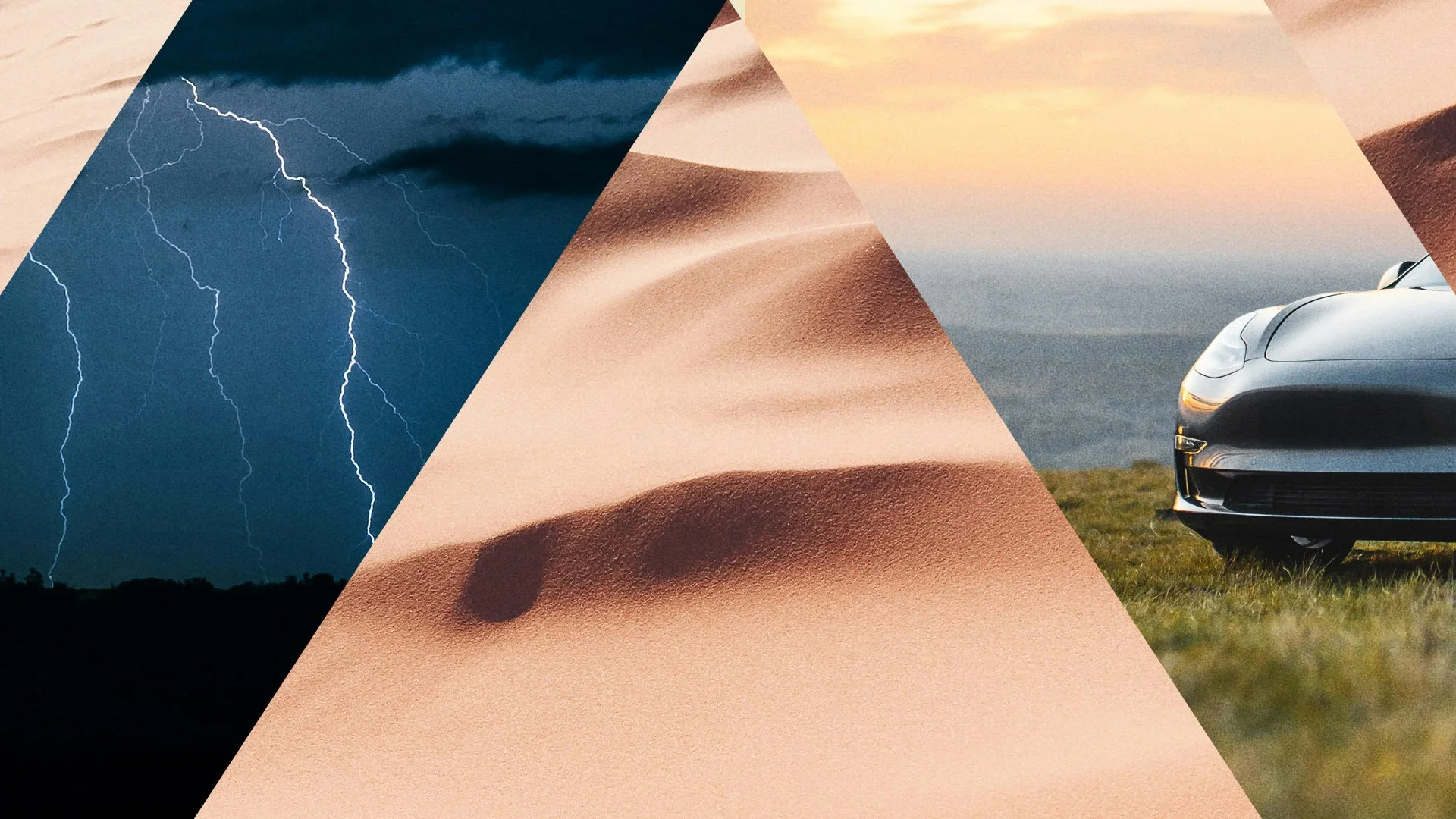
Enabling the next generation
of battery technology.
About Alkalinth
The next generation of batteries offer the promise of carrying twice the charge in half of the space. Alkalinth is focused on producing negative electrode substrates for “anode free” lithium metal batteries. By solving one of the largest challenges of anode free cells - poor Li plating kinetics and low efficiency in initial cycles - Alkalinth is enabling the next generation of battery technology that can be produced at scale in a cost efficient manner.

Lithium metal batteries hold promise due to their inherent high energy density and volumetric efficiency. However, their adoption is limited because of problems with safety due to poor plating kinetics leading to dendrites and mossy “dead” lithium, along with uncontrolled volume change during cycling. Challenges in manufacturing owing to logistics of handling bare Li metal negative electrodes has led to interest in “anode free” cells, but lifetime and performance is even more of a challenge with no seed Li on the negative electrode substrate.
The core high-risk technical problem Alaklinth has solved is a replacement for the simple planar copper foils currently used in lithium metal battery anodes, to enable the benefits of anode free cells while overcoming their limitations. Alkalinth’s proprietary process modifies off-the-shelf planar copper foil into a lithiophilic, functionalized 3D surface using a scalable and low cost method.
The lithiophilic nature of Alkalinth’s material is achieved with a specialized Li rich coating on the surface of the anode. Plating kinetics are improved greatly versus pure Cu, allowing even coating of Li over the anode on charge. The process eliminates the formation of dendrites and dead lithium. The result is improved coulombic efficiencies, leading to better capacity retention and longer cycle life.
Technology
The surface of Alkalinth’s anode is functionalized into a three dimensional structure with the formation of the Li rich coating. The coating can be controlled to form a number of morphologies, each with the potential for unique benefits. Regardless of morphology, the coating develops a high surface area skeletal framework for the Li to deposit into during charging. The effect of this permanent high surface area framework is reduced volume change on cycling, allowing a more resilient SEI layer to form and eliminating the continuous reactions of Li metal with the electrolyte.
Our lithiophilic, functionalized 3D structured anode substrate will allow anode free lithium metal batteries to achieve the highest performance, lowest cost and longest cycle life possible.

Benefits
By replacing incumbent planar foil substrates, our substrate material:
encourages facile kinetics and ensures even, repeatable deposition - resulting in higher efficiencies and longer cycle life;
eliminates battery failures due to dendrite growth, uncontrolled volume change, and the cumulative effects of inconsistent cycling;
achieves increased performance because they are metallophillic and features a functionalized, three dimensional structure;
can be handled the same as planar foils, and will easily integrate into existing manufacturing methods as our substrates are air stable.
is compatible with any electrolyte, separator and cathode configuration.